(3) Design guide
(a) Relationship between shaft diameter & packing box inner diameter/packing width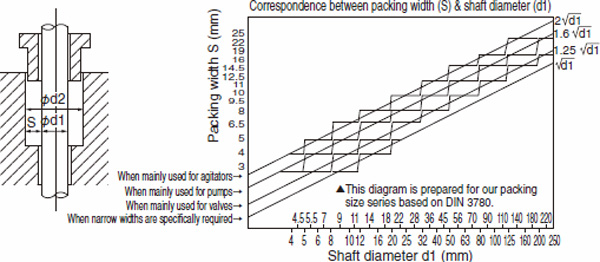
(b) Fluid pressure and number of rings
The number of packing rings to be used normally depends on the pressure of the fluid to be handled. The numbers of rings shown here are intended to serve as a measure for the length of packing to be applied, on condition that a proper packing width is chosen.
It should also be noted that these numbers of rings should be used as reference information, as they vary according to the packing material selected and fluid conditions (type, temperature, peripheral speed), as well as the environmental conditions (with or without cooling jacket, flushing, oil feeding, etc.).
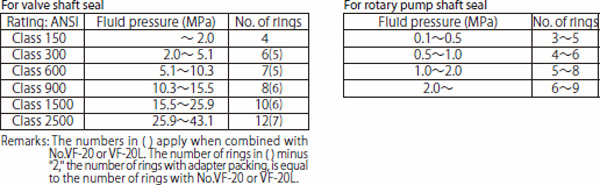
(c)Standard tightening stress of gland packing for valves
The values of standard tightening stress shown below indicate the ones required to satisfy the ANSI hydraulic pressure test.
Use them as a measure for service.
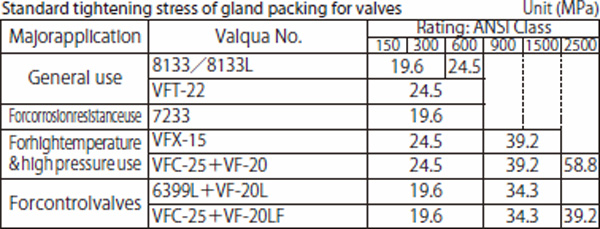
(d)How to use gland packing effectively
(i) Utility of spacer rings
Spacer rings have the advantages of effectively preventing not only the extrusion of packing but also permeation leakage and back leakage as shown in the figure below. Spacer rings are normally used between both sides of packing for the purpose of preventing the extrusion of packing, while they are sandwiched between two pieces of packing for the purpose of avoiding permeation leakage. Also, if spacer rings are used for preventing permeation leakage with two or more types of packing combined, it is effective to sandwich the spacer rings between them. The major materials of a spacer ring are solid PTFE, filler-integrated PTFE, and joint sheet. The thickness of a spacer ring is commonly on the order of 1 to 3 mm.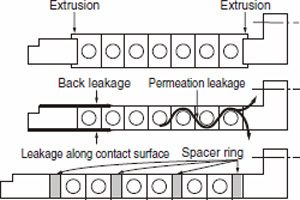
(ii) Recommendation of molded rings
Molded rings not only contribute to reducing the time required for assembling, but also play a critical role in maintaining a favorable sealing property.
When coil type packing is used as it is, the tightening force is hard to convey to the depth. As a consequence, a substantial difference will arise between the gland follower side and the bottom side of the stuffing box, which may cause stress relaxation, resulting in leakage. Particularly for pumps whose tightening force is relatively small compared to valves, the back face of packing cannot be well accustomed to the stuffing box, causing back leakage to occur. To make full advantage of the performance of packing, it is recommended that molded rings be used.
(iii) Anticorrosive treated packing
Graphite based packing may accelerate the corrosion of the mating metal surface with which it comes in contact.
This is due to a potential difference between the graphite (C) contained in the packing and the metal. Which means the graphite acts as a cathode material on the activated anode of the counterpart to increase the current density.
In order to restrict such an activation of metals, our graphite based packing combines appropriate amounts of anode inhibiter and cathode protector to protect metals, thus ensuring the prevention of corrosion under a wide range of service conditions.